“We aimed to make the tour enlightening and illustrate how we are working on solving some complex metal separation problems.”
Bunting Magnetics is one of the world’s leading designers and manufacturers of magnetic separators, eddy current separators, metal detectors and electrostatic separators, with globally located manufacturing facilities.
The YBMR is an important part of the British Metal Recycling Association (BMRA), providing purposeful and educational activities that may assist members in their own career development. Members are generally under the age of 40 and could be working in the yard, the office or the laboratory.
Effective metal separation is a key stage in the recycling process, either to purify a recycled product or to recover valuable metals. The technology continues to evolve with the application of increasing high magnetic fields, using both permanent magnets and electromagnetic fields, and the evolution of new technologies such as electrostatics.
During the morning session, Bunting’s Laboratory Manager Dr. Neil Rowson introduced the extensive range of metal separators presently available, with specific reference to recycling applications. The afternoon session focused on equipment demonstrations, assessing complex material separation challenges presently facing recycling companies.
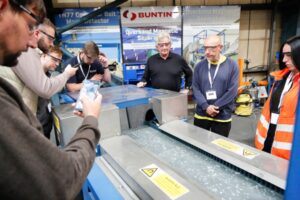
Dr. Rowson showed how separation technology commonly used in the mining and mineral processing industry is being adapted for specific recycling applications. The Magnetic Disc Separator (MDS) enables mineral beneficiation when mining coltan (a dull black metallic ore containing niobium and tantalum) and beach sands, but the high-strength and variable magnetic field mean the technology is also being using successfully for the separation of fine metal fractions found in shredded printed circuit boards. The separated fraction had a gold content of up to 6%, highlighting the value of successfully separated and recovered metal.
The recycling of lithium batteries continues to prove challenging and Dr. Rowson demonstrated the ability of the high-intensity permanent Rare Earth Roll Magnetic Separator to separate weakly magnetic particles. This technology is part of the process developed by the University of Birmingham.
On the ferrite Drum Magnet (model APD), YBMR members witnessed the separation of flat lithium batteries from non-magnetic granules. Removing such lithium batteries from the recycling process reduces the risk of fires. The poor magnetic properties of low-grade lithium batteries, due to a low metal content, proved surprising.
After demonstrating the separation of weakly magnetic particles in a slurry state on a Wet Magnetic Separator, the focus turned to the ElectroStatic Separator. Bunting is a world leader in the development of ElectroStatic Separators and the demonstration showed the separation of small conducing metals such as thin copper wire.
The tour then moved to the heavy recycling test area, with Bunting’s Phil Tree and Michael Allen staging separation demonstrations on the Eddy Current Separator, and the HISC and SSSC Stainless Steel Separators.
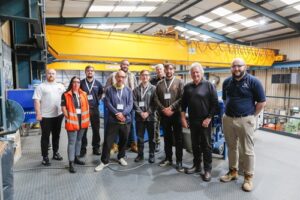
Finally, the YMBR group received a tour of Bunting’s manufacturing facility where they saw equipment, under construction and ready for shipment including two laboratory-scale ElectroStatic Separators, Eddy Current Separators, and Overband Magnets.
“We aimed to make the tour enlightening and illustrate how we are working on solving some complex metal separation problems,” explained Ben Clemett, Bunting’s Area Sales Manager and fellow YBMR member.
Source: Bunting